You have no items in your shopping cart
Improving Vacuum Levels in Short Path Distillation Systems
- Posted on
- By Goldleaf Scientific
- Posted in How To Guides, Short Path Distillation, Vacuum Pump
- 0
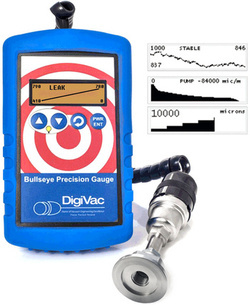
Many users of small Short-Path Distillation systems find they only achieve system pressure levels of 500-1000 microns when they first set up. This post gives step-by-step details on ways to improve system leaktightness, plus properly protect your Vacuum Pump so that deep vacuum (low pressures) under 100 microns can be sustained.
Overview
You must establish what pressure level the vacuum pump itself achieves, then compare that reading to the pressure in the entire system, when empty. We also discuss how to address poor pressure readings at the pump level, and also how to find and eliminate leaks within the Short Path System. This eliminates the perceived need for diffusion pumps or vacuum controllers.
System
Typical setup is: your Short Path Distillation System, with 1L to 5L round bottom, 2-neck or 3-neck top, condenser glassware, fractional connection glassware, vacuum hose connecting to a digital pressure gauge such as Welch 1526K-10*, vacuum hose connecting to the cold trap glassware, which connects to the Welch 1400B-01 DuoSeal Belt Drive Vacuum Pump.
(*for most accurate reading, orient the sensor nozzle vertically, with the nozzle opening pointing down)
Terms used in this post
Vacuum achieved in this system is very deep. 99.99% of all air is removed, and the remaining pressure is a fraction of 1 mm Hg. 1 mm Hg pressure is called 1 torr. 0.500 torr is called 500 millitorr or 500 microns. We may use the term “vacuum”, but we are measuring the slight amount of remaining pressure, and that’s what your vacuum pressure gauge reads.
Your goal is to have your vacuum pump pull below 20 microns, and your system pull below 100 microns or 150 microns.
Leaktightness refers to a connection of hose-to-glassware or hose-to-metal or stopper in flask opening where vacuum leaks could occur and create higher pressure in your system. Identifying those leak sources and taking steps to assure they are leaktight is the key to Leakproofing your system so you can achieve readings below 100 or 150 microns.
100 microns is used as the targeted system pressure because it is well-established that you can fractionally distill Terpenes from your product at around 165°C IF the pressure is this low. At 100 microns or deeper, you can distill THC/CBD at 205-215°C if system pressure starts below 100 micron.
If you can only get your system to, say, 150 microns, you can compensate with slightly higher product temperatures to achieve distillation.
6-inch piece of thickwall, red rubber vacuum hose, 7/16” ID (photo). Note vertical orientation.
Hose Clamps, 2 EA, one at each end of the vacuum hose (photo).
Screwdriver, used to tighten the hose clamps on to the pump inlet and the pressure gauge.
Digital Pressure Gauge, such as Welch 1526K-10, which is part of your Short Path Distillation System (photo).
Vacuum Pump, such as Welch 1400B-01, which is also part of your Short Path Distillation System (photo).
Vacuum Grease, such as Krytox.
You may need more vacuum pump oil, such as Welch #1407K-15 DuoSeal (photo).

Step 1: What is pressure reading AT PUMP INLET?
a. Connect vacuum hose to pump inlet and tighten hose clamp until leak tight.
b. Vacuum gauge sensor nozzle is inserted into the other end of the vacuum hose. It is smaller than the hose ID but tightening the clamp compresses hose onto the nozzle, tighten until leak tight.
c. If you see rubber extruding out to the slots in the hose clamp, you are more than sufficiently leak tight.
d. Turn vacuum pump on and let it warm up for 30 minutes or longer.
e. Then, turn on pressure gauge and wait for the reading to stabilize, which usually takes about 3-5 minutes.
f. If the pressure reading is below 20 microns, you have a properly performing vacuum pump.
(The reading on the 1526K-10 gauge in the photo above is 0.055 torr, which is 55 microns.)
g. If the pressure reading is above 20 microns, change the oil but ONLY once the pump is warmed up. Never change oil on a pump that is not fully warmed up.
h. Once old oil is drained, refill with a good quality oil. Welch DuoSeal Oil 1407K-15 (gallon) is recommended. Grade 19 oil and similar are not sufficient; poor quality oil is susceptible to oil vapor loss and rapid breakdown. Contact us if you need more details on steps to change vacuum pump oil.
i. Once again, with fresh, good-quality oil, turn on the pump and let it warm up for 30 minutes or longer.
j. What is the reading this time? If still not below 20 microns, contact us for guidance on ways to improve vacuum pump base pressure.
-------------------------------------------------
a. Disconnect the vacuum hose from the pump inlet and disconnect the vacuum sensor from the hose. Re-install the vacuum sensor to its original connection in your Short Path Distillation System (“System”).
b. Reconnect your vacuum pump to your Cold Trap and use coolant (such as dry ice in ethanol) to cool the cold trap. Cold Trapping is required to protect your vacuum pump, and it also provides better pressure readings.
c. Make sure all connections are sealed and turn on your vacuum pump.
d. Take vacuum pressure readings only once the pump is warmed up (30 minutes or longer). Remember, readings can require 3-5 minutes or so to stabilize.
e. What is the vacuum pressure reading in the System? If 100 microns or lower, congratulations! You have a leaktight system.
f. If your System reading is significantly higher when using a vacuum pump that reaches 20 microns or lower, then you have one or more VACUUM LEAKS in your System, and you must become a Leak Detective to identify and eliminate each leak.
g. See the checklist below that addresses all the connection points that might be leak sources.
- Stopper in Round Bottom Flask opening should have a thin layer of vacuum grease applied for leaktightness.
- Condenser joint inserted into Round Bottom Flask opening should also have a thin layer of vacuum grease.
- Thermocouple setup inserted into RB Flask opening usually does NOT use vacuum grease. There should be an elastomeric ferrule on the metal stem of the thermocouple as it passes through the stopper, with a top that tightens to assure leaktightness.
- Condenser vacuum port to cold trap port: probably 3/8” ID vacuum hose; if using ½” ID hose, use hose clamps to compress hose for leaktight connection. We recommend using a single piece of hose.
Gauge vacuum port to vacuum sensor. Again, probably 3/8” ID vacuum hose but can use ½” ID hose.
If you have a 3-way valve setup on any hose, we recommend you check for leaktightness. Threaded metal valve setups with PTFE tape are almost always NOT vacuum tight.
Cold Trap vacuum port to vacuum pump inlet: use ½” ID vacuum hose and use hose clamps to compress for leaktightness.
Metal vacuum valves or any other component that has screw threads is a prime candidate for leaks. Contact us for alternative connection types.
Being a “Leak Detective”
You can also use your vacuum gauge to be a Leak Detective by once again inserting the vacuum sensor nozzle into your 6” vacuum hose setup and clamping leaktight. Disconnect System hose connected to the cold trap as the first connection point away from the vacuum pump. Connect the hose/gauge setup (“Testing Setup”) at that point on the cold trap. Tighten the hose clamp so you have a leaktight Testing Setup. Orient gauge sensor vertically. Your readings at this first point will tell you if the cold trap connections are leaktight.
You can take a pressure reading using your Testing Setup at each successive connection point to identify which ones are sources of vacuum leaks. You can then address ways to make the leak points more leaktight.
Again, threaded metal components are a prime spot for leaks. Sealing with PTFE tape is NOT sufficient, such tape is porous under vacuum. Loctite PST and similar pipe sealant pastes are better choices if you cannot eliminate threaded connections. Although more prone to breakage, glass valves and connections offer greater leaktightness when properly installed.
Vacuum Controllers and Diffusion Pumps
Owners of Short Path Distillation Systems often assume they must use vacuum controllers to achieve deeper vacuum. Vacuum controllers can only control vacuum ABOVE the pressures achieved in your System.
Others assume that their vacuum pump setup must be reach even deeper vacuum levels to overcome leaks, by using Diffusion Pumps mated to their Welch Vacuum pumps. This setup is probably unnecessary in a leaktight system, and if the system is not leaktight, deploying a diffusion pump probably will not overcome the leaks and provide the deep, sub-100 micron System pressures you are targeting.
Again, leakproofing your System can be your first, best approach to achieve pressures you want.
Comments
Be the first to comment...