You have no items in your shopping cart
What is the Purpose of a Vacuum Pump
- Posted on
- Posted in Vacuum Pump
- 0
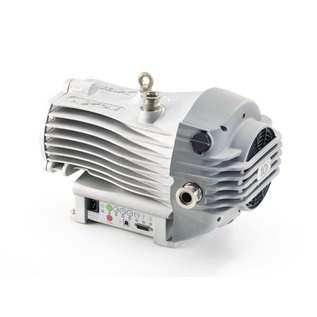
To successfully process component parts in a vacuum furnace (Fig. 1), we need to create and control the “atmosphere” surrounding the work. In general, applications run in vacuum furnaces can be broken down into five main (5) categories1:
- Processes that can be done in no other way than in vacuum;
- Processes that can be done better in a vacuum from a metallurgical standpoint;
- Processes that can be done better in a vacuum from an economic viewpoint;
- Processes that can be done better in a vacuum from a surface finish perspective;
- Processes that can be done better in a vacuum from an environmental perspective.
Figure 1 – Vacuum Annealing of Copper Heat Sinks
A principal difference between vacuum heat treatment and all other forms of thermal processing is the absence of, or perhaps better stated, the precise control of surface reactions. In addition, vacuum processing can remove contaminants, and under certain circumstances degas or convert oxides found on the surface of a material.
Typical vacuum applications include industrial, food and packaging, coatings, analytical and medical technology, solar, semiconductor technology and research and development. In the heat-treating industry typical processes involve:
- Brazing
- Hardening
- Annealing
- Case Hardening (e.g. carburizing, nitriding)
- Sintering
- Tempering
- Special Processes (e.g. degassing, diffusion bonding)
Choosing the Proper Vacuum Level
In order to create a vacuum within a vacuum furnace (Fig. 2), we need to remove the molecules of air and other gases that are present inside by means of a vacuum pump. The level of vacuum required (Table 1) is that which demanded by the application being performed.
Figure 2 – Typical Single Chamber Vacuum Furnace Pumping Package
The more molecules that are removed from a vessel, the better the vacuum. The quality of a vacuum is described by the degree of reduction in gas density, that is, gas pressure. In the field of heat treatment, we typically conduct our processes in the low, medium, high (and in some rare cases ultra high) vacuum levels (Table 1). The majority of applications are processed in the high vacuum range. By contrast, at 200 miles above the earth, the vacuum in space is 1 x 10-8 Torr. At 400 miles it is 1 x 10-10 Torr and in deep (or outer) space is 1 x 10-16 Torr.
Table 11 – Classification of Vacuum
Notes:
[a] The SI unit of pressure is the Pascal (1 Pa = 1 N m-2)
[b] Standard atmospheric pressure of 1 atmosphere is 101,325 Pa or 1013 mbar (1 bar =105 Pa)
[c] Standard atmospheric pressure of 1 atmosphere is 760 Torr (1 Torr = 133.3 Pa)
[d] Ultrahigh vacuum is defined as the pressure range between 10-6 Pa (Europe) and/or 10-7 Pa (USA) to 10-10 Pa.
The vacuum vessel and pumps (e.g. mechanical, booster, diffusion or turbomolecular, holding) together with the associated piping manifolds, valves (mechanical pump, high vacuum isolation, vacuum (brake) release, backing), vacuum measurement (i.e. gauging) equipment (molecule counters) and traps comprise a typical vacuum system.
Selecting a Vacuum Pump
The selection of a proper vacuum pumping system (Fig. 3) is highly application dependent and is complicated by the wide variety of operational, process and equipment issues. In many instances, the furnace and pumping system are pre-existing and we have little choice other than to operate at a predetermined vacuum level. Irrespective, each system must meet a specific set of requirements that are imposed by the process and production requirements. These requirements ultimately determine the size and type of pumps needed for the successful operation of the system.
Figure 3 – Family of Vacuum Pumps (Photograph Courtesy of Edwards Vacuum LLC)
Among the process variables, which should be known before attempting to size or select a pumping system, are the internal volume of the vacuum vessel and components, the time and pressure required and the size of the gas load that must be pumped off. In an ideal world, we know the answers to all of these questions. In the real world, we often compromise by applying safety factors to allow for the uncertainty of the information available.
Vacuum furnace pumping systems typically consist of various subsystems; namely, the roughing pump, the vacuum booster pump set and the diffusion pump. These pumps fall under the categories of mechanical pumps and diffusion (vapor) pumps. Specifically:
- Roughing pumps (i.e., mechanical pumps and blowers) are used in a vacuum furnace’s initial pumpdown phase from atmospheric pressure down to an intermediate vacuum pressure level. In many heat treatment processes, one or both of these type of pumps are adequate for the application.
- Diffusion pumps are used when it is necessary to generate a system pressure less than the pressure normally generated by a mechanical pump and booster package alone.
Vacuum pumps should be started (and stopped) in a particular sequence. Having a defined pump startup sequence (Fig. 4) and chamber evacuation procedure (Fig. 5) is highly recommended (and will be explored in detail in future articles in this series).
Figure 44 – Typical Pump Startup Sequence
Figure 54 – Typical Chamber Evacuation Procedure
Vacuum Effects2
The effects of treating components in a vacuum are (1) in the medium-high vacuum region the partial pressure of the residual air (i.e., oxygen and water vapor) in the furnace is significantly reduced and will provide an environment to process components with little or no surface oxidation and (2) decomposition of existing oxides in the surface of components may occur depending on the temperature and material type.
Ways to Help Pumping Efficiency
Individuals familiar with vacuum furnaces know the importance of having an absolutely leak-tight vacuum chamber, doors, feed-through, and penetrations. For critical applications, such as processing of superalloys or reactive metals, a leak rate of less than 5 microns/hour is mandatory. For normal vacuum applications, the leak rate should not exceed 10 – 20 microns/hour. Even a slight air or water leak will overwhelm the vacuum pumps and cause the vacuum level to rise several decades in pressure. Proper attention, therefore, must be given to the entire vacuum system and leak detection of all joints, welds, seals, valves, and pumps as well as the vessel itself is critical.
An important operational consideration is to limit the amount of time a furnace chamber is exposed to room air, either during loading/unloading or when the unit is not in production. The effects of humidity (water vapor) are often devastating to the pumping system, decreasing its efficiency and creating an oil/water mixture in the pump that requires the pump to be ballasted. When not in production, vacuum furnaces should be pumped down to several hundred microns and then isolated from the pump set.
Finally, moisture trapped in the hot zone or heat exchanger tube bundles (if internal) is extremely difficult to overcome by pumping alone. Often times backfilling with nitrogen, or if available, argon will help minimize this effect.
Pumping speed refers to the volume flow rate of a pump at its inlet, often measured in volume per unit of time. Throughput refers to the pumping speed multiplied by the gas pressure at the inlet and is measured in units of pressure-volume/unit time. At a constant temperature, throughput is proportional to the number of molecules being pumped per unit time, and therefore to the mass flow rate of the pump.
Summary
Understanding your application requirements is an important first step in the choice of the right vacuum pump system. Remember, more is not necessarily better and selecting the proper combination of pumpdown speed, efficiency and performance are all important. Future installments in this series will investigate many of the issues involved with pump selection, pump maintenance and pump operation both from a practical and a scientific perspective.
References
- Herring, Daniel H., Vacuum Heat Treatment, BNP Media Group, 2012.
- Sobiegray, Dave and Dick Amos, “Developments in Vacuum-Pumping Technologies for Vacuum Metallurgical Processes”, Industrial Heating, September 2009
- Collins, Don., “Choosing Process Vacuum Pumps”, CEP, August 2012.
- “The Vacuum Furnace Process Application Note”, Eurotherm Ltd., 2005
- “Keeping your Vacuum Furnace Pumping System in Optimal Condition”, Ipsen International, AZO Materials, 2014.
- Wikipedia (www.wikipedia.org)
- Steel Heat Treatment Handbook, 2nd Edition, George E. Totten and Maurice A. H. Howes (Eds.), Chapter 7: Vacuum Heat Treating, Marcel-Dekker, 1997.
- Brunner Jr., William F., and Batzer, Thomas H., Practical Vacuum Techniques, Robert E. Krieger Publishing Company, 1974.
Comments
Be the first to comment...